Burrs |
Burrs are material which remains after processes, like grinding, polishing, pressing. Size and kind of burrs are various according to kind and performance of the machine. Burrs have some popular names like "grinding burrs", "polishing burrs" due to process, or "whisker burrs" due to its shape. Burrs are often harmful for products. It is said that there is the industry, whose complaints (about non-conforming items) after delivery are mostly caused by burrs. It is often said that even if burrs don't affect property of the products, they are disliked because worker may get injured at assembly. |
|
Deburring process |
There are many deburring processes and each process has both merits and demerits, just as our SEP Processing. Merits or demerits varies according to understanding. For example, if sharp edge is desired on deburring, the process with making round will be avoided. On the other hand if round edge is desired, the process will be accepted. |
|
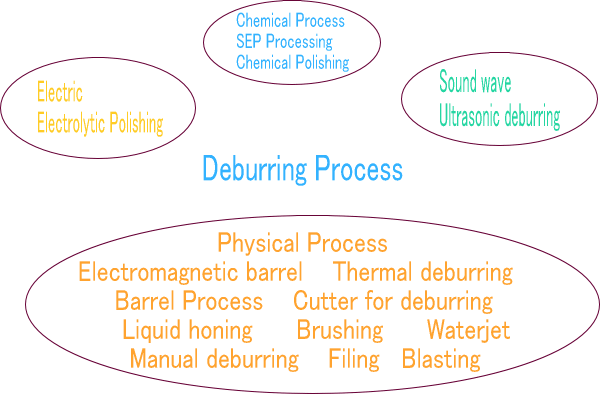 |
Satisfying you without showing it |
Any plant tour is not allowed because the process method and process fluid are our own know-how of SEP Processing. But visit to our company is quite welcome. We'll have discussion with you about purpose of process at the meeting room, and perform SEP process while you wait. After we get the result of processes, we'll fix the condition of process to meet your requirements, such as additional process, change of process fluid, etc. About this selection of condition, some customer says to us in delight that "You may satisfy us without showing the process." |
|
Short story |
Our businessman may say that "SEP Processing is not almighty." There are many processes as above, each process has both merits and demerits. Merits or demerits varies according to understanding. For example, if sharp edge is desired on deburring, the process with making round will be avoided. On the other hand if round edge is desired, the process will be accepted. So, we tell customer what we can do and can't do to meet customer's requirements. |
|
What's SEP Processing |
SEP Processing is a technique of deburring by chemically melting the product. We immerse the product in special process fluid (SEP Processing fluid) which melt the product. |
|
Features |
*No physical external force is applied to the product because we only immerse it in fluid. So there is no deformation, dent, and distortion even if the product is thin plate. *Surface roughness will be improved because fine crack and unevenness at surface will be removed and become flat. (Some materials cause roughness of the surface.) *As it is fluid, process will be performed uniformly. Inside the very fine pore can be polished if the fluid can infiltrate. *SEP process also can apply to the place where can't reach tool because of deep hole or groove at complex shape. *Dimension variation between before/after processes can be controlled in micron unit. *No initial cost is needed because it is manufactured by commissioning (Process is performed at our company). *As it is fluid process, SEP process is promising as an alternative technique of precision cleaning (removal of contamination, dust). *It's easy to take steps for change of process because it's only to melt surface of metal. |
|

|
Explanation |
*SEP Processing is a technique to remove burrs using chemical reaction by immersing the product in the special fluid.
*Because the base of burrs are deformed, burrs are affected by chemical reaction more than other parts.
*As burrs commonly have less thickness than its height, burrs will drop only by melting product surface as much as their thickness.
Sharper burrs will be removed faster than flat parts because amount of melt is larger. |
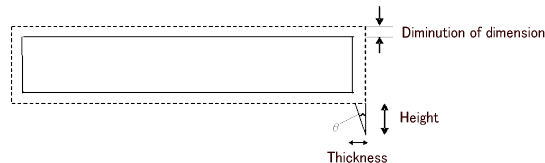
|
Fine burrs removal process |
Burrs removal model by SEP Processing
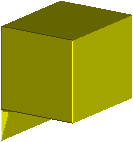 |
 |
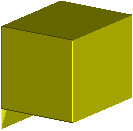 |
Before process Burr is seen at bottom, left side of the product. |
|
Process 1 Burr gets slightly smaller. |
|
|
 |
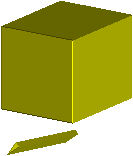 |
 |
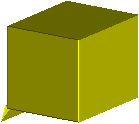 |
Process 3 Burr completely drops from the product. (Fine burrs were melted) |
|
Process 2 Burr is likely to drop from the product because joint becomes thin. |
* Given the above, the important factor about removing burrs by SEP Process is not a height of burrs, but a thickness of joint. |
|
 
|
Request of trial production |
Who |
What to do |
How long does it take |
You |
1. OR Please let us know about purpose of process, material, size, numbers of product by mail. We'll consider carefully whether we can process, and get back to you soon.
|
a few minutes |
|
if we can process
 |
|
Carrier OR You |
2. to Please send the product to us. |
1 day |
|
 |
|
SEP Co.,Ltd. |
3. Select process condition or Examine mass-production method |
Approx. 3 - 7 days |
|
 |
|
SEP Co.,Ltd. & Carrier |
4. 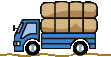 to Return the product applied SEP Process with picture data. |
1 day |
|
 |
|
You |
5.     Please consider whether you go to mass-production or not, based on the processed product and picture data. |
? |
|
 |
|
People all over the world |
6.   
Products applied SEP Process are used in various fields. |
|
|
Add-on of trial |
We have an epigram that "One trial is better than hearing!" That is, we think one trial of our SEP Processing make you more understood than many explanations. Please experience our technique by your product. We are certain that our technique will please you.
|
|
 |